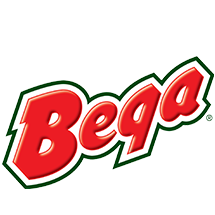
The Bega Group includes the Bega cheese business, Tatura Milk Industries and Bega Foods incorporating the business formerly owned by Mondelez Australia (Foods). The Bega Cheese Group is home to many trusted and wholesome food brands enjoyed in Australia and around the world.
Bega has grown to be a successful ASX listed company with a turnover in excess of $1.5 billion, and over 2000 employees. With a strong position in the Australian consumer goods market, Bega includes well-known brands such as Vegemite, Farmer’s Table and Bega Peanut Butter.
Bega Cheese’s processing and packaging unit produces 50,000 tonnes of value-added cheese products including cheddar cheese retail packs and processed cheese products as well as individually wrapped slices and slice on slice products for food service outlets.
What challenges were you experiencing prior to purchasing MEX?
Prior to implementing MEX, we struggled with a stagnate system. We needed a program that could be modified to suit a variety of maintenance tasks. Through our experience we’ve learnt that implementing a one size fits all approach to maintenance does not yield any improvements and so we needed a program that could be versatile and personalized on a task to task basis.
We also struggled to adequately store information relating to our assets’ paperwork that kept piling up, making it a challenge to keep everything together. Our old system didn’t allow for the attachment of work approvals, images or documents to the pertaining asset. This left us with an incomplete overview of our maintenance and assets making it difficult to make informed decisions on how best to approach maintenance.
What made MEX stand out against our competitors?
Several MEX features stood out as a point of difference when compared to other CMMS systems. MEX offered us the flexibility to have a portable and personalized maintenance system. The MEX iOS app, customizations and custom reports available were therefore a big draw for us.
The MEX system offered a user-friendly approach to maintenance practices and amongst other things, was a simple to use maintenance scheduling tool and request approval function. This allows us to plan our maintenance with ease and forecast work going forward.
One of the main features that stood out was the Preventative Maintenance (PM) structure in MEX. This set MEX apart from the rest and gave us the ability to easily generate PM plans to assist in the reduction of equipment failure and further our maintenance goals of maximizing manufacturing uptime.
What did your decision-making process look like? Were there any factors or features that you considered heavily?
Yes, there were four factors that reinforced our decision when looking to purchase MEX.
- MEX Support meant we would always have assistance throughout our use of MEX
- Custom Reports that could be self-created by us or supported and created by MEX
- Integration with our pre-existing finance software meant a more seamless transition
- The ability to move towards a paperless work-flow
What Benefits have you gained from using MEX?
Since implementing MEX, we have seen a dramatic decrease in our paper usage and the majority of our day to day tasks are now computerized. This now eliminates double handling and reduces the risk of losing data. MEX being paperless allows us to digitalise all maintenance information giving us a comprehensive library of data in one location. This makes it simple to report on practices and look for areas where we can improve maintenance processes.
Can you give a specific example where you feel MEX has led to a return on investment?
At Bega we really struggled with copious amounts of permits within work orders. Prior to MEX this was an entirely paper-based system that was nearly impossible to administer, the processes were lengthy and frustrating. Now thanks to MEX, all the right information is completed, stored and reported on. We’ve seen a clear return on investment through the significant reduction of administration hours allowing us to focus on more important tasks. MEX gives us the comfort of knowing that the system will produce and store work permits for current and future purposes.
Contact the MEX Sales Team today for more information on the Bega Case Study or call + 61 7 3392 4777
This Case Study was last updated: 29/07/2019 08:07