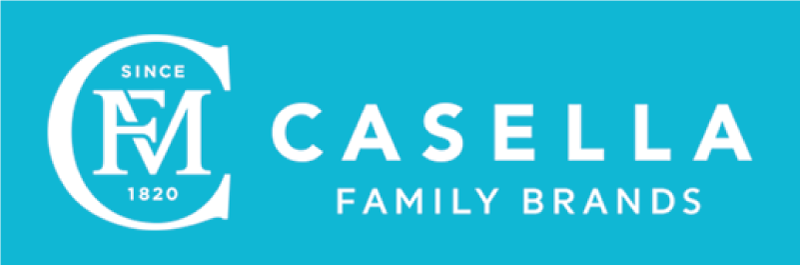
The Casella Family Brands journey began when founders Filippo and Maria Casella immigrated to Australia in 1957, bringing with them a family legacy of wine making dating back to 1820, a deep understanding of wine and a passion to launch a prosperous family business. This successful combination lead to the creation of a thriving family vineyard and winery.
Casella Family Brands is now the largest wine maker of exported product in Australia producing in excess of 140 million bottles per annum with an average output of 55 containers per day leaving the site to supply the world market.
Brands such as [yellow tail], Peter Lehmann, Brand’s Laira, Casella, Young Brute and Morris Wines have all contributed to Casella Family Brands Winery.
In addition to the Yenda based winery Casella Family Brands is also responsible for the production of Yenda & Alehouse through a joint venture partnership with Coca-Cola Amatil. Yenda, Alehouse and numerous imported beers make up approximately 10 – 15% of the Casella Family Brand output.
What are your maintenance goals?
Here at Casella Family Brands we run a large-scale operation with about 700 full time staff, 90 of which work in our Yenda maintenance facility and are responsible for maintaining approximately 10,000 odd assets. Asset maintenance is an integral element in our overall business mandate, our ability to continually produce and supply products to the global market resides in our equipment’s capacity to function effectively and efficiently.
Our key maintenance objectives are to:
- Perform cost effective maintenance practices across all areas of our sites.
- Conducting ourselves at a best practice level of: safety, quality & reliability.
With the overall goal of ensuring the long-term viability of the assets & the manufacturing plant.
How is MEX used?
MEX is heavily integrated into our operation and is utilised as a means of achieving our maintenance objectives. To ensure the long-term viability & reliability of our assets MEX is used day in and day out to monitor and record all elements of our asset’s life-cycle.
All of our production staff are required to install MEX Requests, we have a total of 130 users and produce approximately 700 Work Orders per week. Indexed in the MEX Stores we also have 14,000 spares parts with an estimated value of 9 million dollars that are catalogued & distributed from 7 stores on site.
All Work Orders are detail orientated and we include all parts and labour used which allows us to keep abreast of all current work whilst contributing to the asset’s history enabling quality maintenance practices. We also link all certification, plans, manuals & documents to the asset with which it belongs.
To maximise cost effective maintenance practices and increase equipment safety and reliability, we aim to minimise any unscheduled equipment downtime. All preventative, proactive & condition monitoring work is carried out through the Preventative Maintenance module helping us achieve our quality assurance goals.
We understand that even with the most robust Preventative Maintenance schedules, reactive maintenance is still an unavoidable evil so all breakdown or reactive work is recorded & analysed through the MEX System. Recording this data provides us with the necessary information to implement strategies to avoid any breakdowns in the future.
What benefits have you seen since the implementation of MEX?
MEX was implemented on site in 2007 and it has since proven to be a beneficial investment across all sections of the maintenance & engineering departments.
Some of these benefits include:
- The robust & easily manageable nature of MEX means it’s able to be implemented at all levels of competency throughout the workforce maximising the benefits of MEX.
- We now have the ability to control and modify practices to drive efficiencies of the maintenance function and the production throughout our operation.
- MEX gives us the ability to set up effective working structures of assets & build a strategic plan which suits the area it is designed for.
- The ability to attach all related parts documents & historical information to tailor a fully scheduled maintenance plan within budgetary requirements.
- MEX has helped within its design to give us a separated structure within the Casella group in order for the departments to run independently & yet still be able to use all the attached structures.
- High level reporting of KPI’s & daily reports enables us to monitor and manage all levels of maintenance.
Contact the MEX Sales Team today for more information on the Casella Family Brands Case Study or call + 61 7 3392 4777
This Case Study was last updated: 25/11/2016 13:11