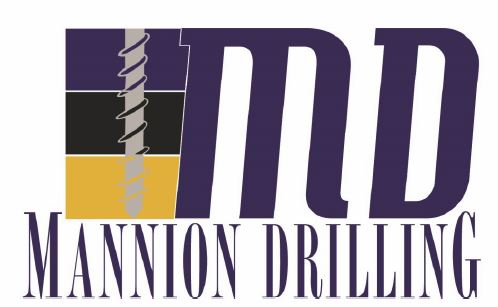
Mannion Drilling is a family operated company located in Gunnedah specialising in providing leading edge water and mineral exploratory drilling services to both the public and private sector including government, mining and agricultural projects across NSW. The company offers services such as water bores with NSW artesian water well license through to mineral exploration holes. Mannion Drilling covers a variety of different types of drilling from Diamond Drilling, Rotary Mud, Reverse Circulation Drilling, Hammer Drilling, PCD Drilling and Field Inspections, just to name a few.
Why did you choose to purchase MEX as your CMMS?
Mannion has several primary objectives that we need to achieve with a CMMS system. These include:
- Improving asset control
- Managing stock purchases and inventory
- Developing robust maintenance records and access real time reporting
All with an aim to maximise workshop/stores ROI and improve administrative efficiencies.
MEX was selected over other providers as we felt the system ticked all these boxes. Not to mention, the MEX system is adopted largely by mid to large companies from the mining, transport and manufacturing industries which gave us confidence that we could also find success with the system.
MEX provides features that is required for both divisions of the company and has a Dashboard that would help with integration into all types of staff. Particularly for workshop crews who, by nature of their trade, may not be very tech savvy.
Furthermore, being a complete Australian owned and based company means that Mannion Drilling has access to a high level of local supports. The cost for MEX was also on par with other CMMS solutions with comparable features and supports.
How did you find the sales process?
The decision to invest resources in a CMMS was a big step for Mannion Drilling and we wanted to make sure our investment was a good fit for our current needs and robust enough to grow alongside us.
MEX’s Scott Ralph took the time to consider our business needs to ensure that MEX was the best CMMS option for us. He was very focused on making sure our investment was solid and that we would be happy with our decision long term.
We found the Sales Team to be highly attentive and keen to talk through our long list of questions. Once the decision was made to purchase MEX, the procurement process was seamless and efficient. We were teamed up with a trainer and were ready to roll within weeks.
What are your future plans with MEX?
The last 24 months has seen a considerable expansion for our company, with a focus on implementing solid business systems to ensure our business model remained strong and we were well equipped to support future growth. The MEX system will provide the framework to manage preventative maintenance on our major plant and assets.
Being in a highly regulated industry, MEX’s maintenance tracking functionality will be incredibly valuable in forecasting service and inspection schedules. Making sure we maintain industry compliance at all times and ensure our equipment is safe and reliable.
Within the next 6 months, we will expand the application of MEX to include Stores and Inventory Management. Implementing the Stores Module will allow us to better control stock levels and ensure spares required to undertake maintenance are available when needed to prevent unnecessary downtime. The beauty of MEX is that we will also be able to cost out parts accurately to jobs and account for costs associated with maintaining plant and assets or undertaking a specific project.
Contact the MEX Sales Team today for more information on the Mannion Drilling Case Study or call + 61 7 3392 4777
This Case Study was last updated: 18/11/2019 07:11