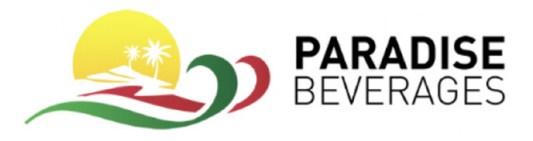
Paradise Beverages (Fiji) Limited formerly known as Foster’s Group Pacific and Carlton Brewery Fiji was a former Carlton United Breweries majority owned subsidiary in Fiji. Today, Paradise Beverages Fiji is owned by Coca Cola Amatil after takeovers of CUB and Foster’s by the SAB Miller Group. Paradise Beverages Fiji is the only local producer of Beers and Spirits in Fiji and employs around 300 people in our two Fijian plants (a brewery and a distillery) and around 120 people in our Samoan Brewery, brewers of Vailima beers. Fijian brands include Fiji Bitter, Fiji Gold, Fiji Premium and Vonu Beer on the beer portfolio and Bounty Rum, Fiji Rum Co, Ratu’s Rum and other assorted minor brands are spirits made by Paradise Beverages in Fiji.
Why did you choose MEX?
We were introduced to the MEX Maintenance Software through the CUB Engineers who were seconded to our Fiji Breweries in the late 80’s.
How is MEX Used?
MEX is used to schedule maintenance for all our critical equipment, track jobs carried out and account for spare parts usage at our Plants. It also helps us map out and plan all upcoming jobs for all our machinery at each of our three plants in Fiji and Samoa. Through MEX, we have built a comprehensive history of work done as well as work outstanding on critical assets.
On top of this we also use the MEX Stores module to control plant and equipment spare parts stock levels as well as movements. MEX has allowed us to accurately track inventory levels and effectively organise and carry out stocktakes on a regular basis. This enables us to carry adequate stock at all times so downtime can be avoided.
What benefits have you seen from using MEX?
With the help of the MEX Maintenance Software, carrying out our routine maintenance has become a breeze. With the click of a button, work orders are raised, assigned to the appropriate personnel and all labour, parts used and time spent on the job are tracked and logged into MEX.
With Inventory Management, take the management of receivable of spare parts by part number for example. We would have spent a lot of time in the past checking the shelves of our stores and manually counting stock each time to enter into stock cards which was a tedious and incomplete process. With the help of MEX, we are able to reorganise our spare parts and other materials storage in the Stores module complete with proper coding to assist tracking of all items as they come in and as they are used in a job.
MEX has helped us free up valuable time and man power in managing our stores. We are able to better manage our spare parts holding levels and quickly resolve our ordering of required items.
The MEX Reporting Module gives us the tools to extract data for asset management as well as design our own reports. We are able to extract details of equipment maintenance costs, labour hours and costs, spare parts and materials usage costs as well as stock holding for an individual plant or consolidations of all plants more easily.
Contact the MEX Sales Team today for more information on the Paradise Beverages Fiji Case Study or call + 61 7 3392 4777
This Case Study was last updated: 04/11/2015 08:11